The use of plastics for medical devices and other applications in the health industry has many advantages and is revolutionizing the way we use them.
ARaymondlife designs and manufactures customized primary and secondary packaging and has positioned itself as a CDMO in the design of tailor-made solutions in response to the needs of the customer.
Comprehensive project management
Relying on its specific skills in plastic processing, the management of complex processes (such as the injection of PEEK (Polyether Ether Ketone)), the integration of active ingredients in an impregnated matrix, together with its knowledge of assembly and welding technologies, ARaymondlife offers comprehensive support to its customers' projects, from the identification of the need to mass production
A project manager is appointed for each project. A multidisciplinary team assists the PM for the design, industrialization, methods, quality development and regulatory affairs. Project management includes the 4 qualification steps DQ/IQ/OQ/PQ.
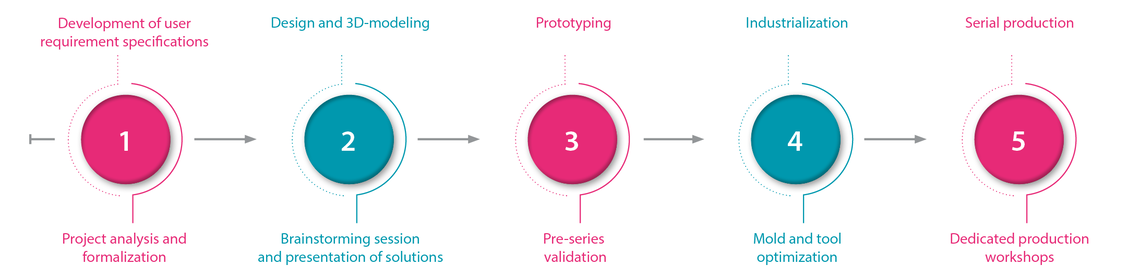
Dedicated engineering office
ARaymondlife has an integrated design office which is involved in each stage of new product development.
Knowledge of the health sector and its requirements is a prerequisite in meeting customer expectations for tailored solutions that implement expertise in materials, fastening and assembly systems, and knowledge of the different modes of sterilization.
The project teams rely on creativity and innovation to design either ARaymondlife branded products or products customized for customers in compliance with the relevant international regulations.
My knowledge of medical grade materials, injection and assembly technologies as well as sterilization methods allows me to adapt to the health requirements and specificities of each new project
Intellectual Property
Before and during the design phases, ARaymondlife conducts prior art search and ensures the freedom to operate for the solutions developed and to see if they are potentially patentable.
Mold making process
ARaymondlife has a vertically integrated tool making capability, with expertise in the design and manufacture of stainless steel molds, coated molds, molds for bi-injection and multi-cavity molds. The design and industrialization departments work in partnership from project conception to commissioning to ensure the optimum tooling and manufacturing solution.
To maintain an optimum level of quality regular maintenance is carried out in house, (molding machines, molds and assembly machines).
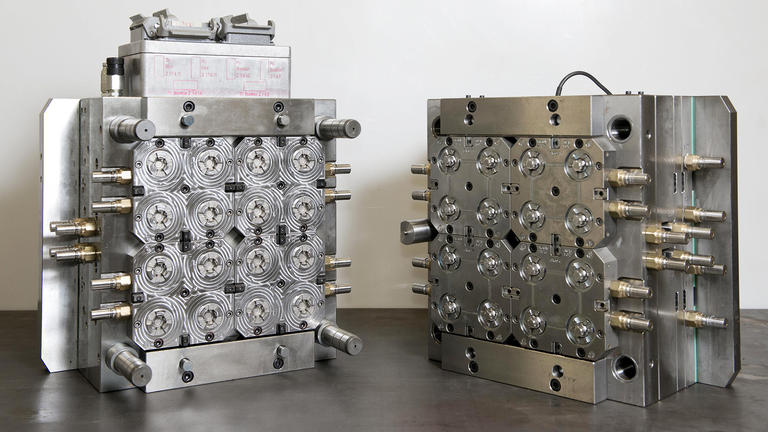
Medical Device packaging
ARaymondlife develops innovative packaging for medical devices and particularly for implants. The expertise in the processing of specific materials such as PEEK also offers many opportunities for implant manufacturers who are looking to transfer the manufacture of their implants from machining to plastic injection.
A packaging solution for implants
Maintaining sterility and traceability of implants during surgery is an absolute necessity to preserve the safety and health of the patient.
ARaymondlife has developed a multi function packaging for implants:
- Ensure optimal protection of the implantable device
- Maintain sterility and traceability
- Facilitate storage and handling of the implant in the operating room
OR2Pack®
ARaymondlife's packaging solution offers a double sterile barrier and allows staff to transfer implants safely from the non-sterile area to the sterile area in the operating room. Manufactured in an ISO 5 clean room, this packaging is suitable for different types of implants and is available in several sizes.
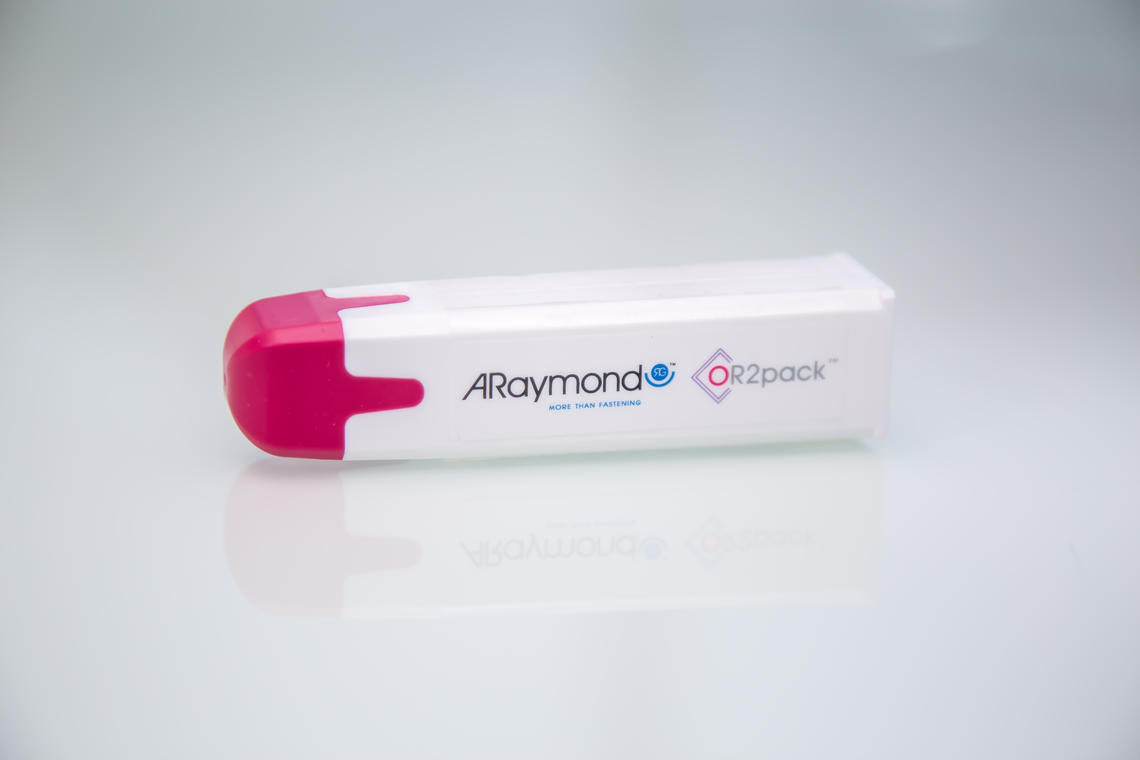
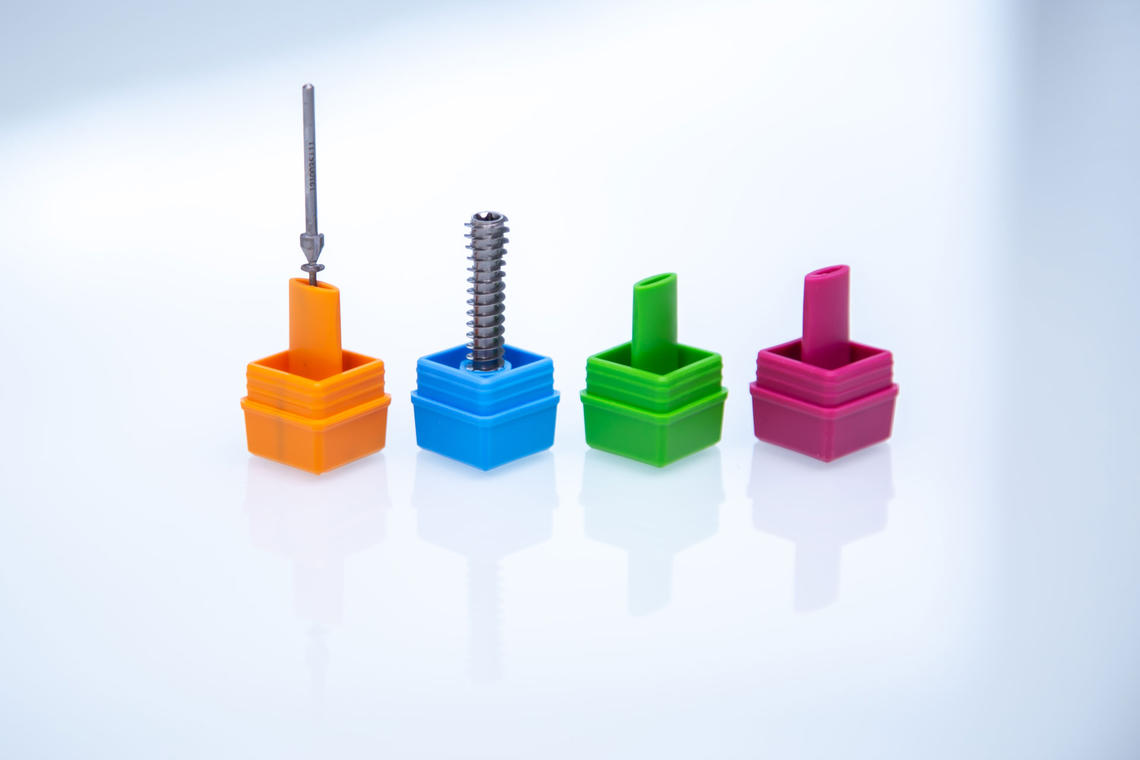
Our specificity is to be able to design an exclusive solution for one customer or an own brand-name product for several customers.
Certification - NF EN ISO 13485: 2016
ARaymondlife is certified NF EN ISO 13485: 2016 for the manufacture of medical devices. This standard sets out the requirements of the quality management system that the company applies to the manufacture of products and associated services.
Download the PDF file
Certification ISO 13485
CDMO activity
ARaymondlife's expertise is based on the design and manufacture of plastic injection molded parts, with key expertise in the processing of USP Class VI materials and specific materials such as PEEK.
The company is developing its Contract Development and Manufacturing Organization activity focused on the development and industrialization of innovative packaging for pharmaceutical laboratories, medical and cosmetics manufacturers.
A tailor-made connector
Virbac has teamed up with ARaymond, a leader in fluid connectors, to develop the connection for the Farmpack™ bag.
Relying on its expertise in this field, ARaymondlife designed a tailor-made solution based on the E-Lock. This simple and ergonomic connection, based on an ARaymond patent for automotive application, has been modified and raised to pharmaceutical quality standards.
This device is integrated into an innovative bagpack designed to safely administer antiparasitic treatments in breeding heards and flocks.
Both removable and reusable, this connector eliminates the risk of leaks and waste of drugs. The E-Lock and Base solution allows 360° rotation and gives the user great freedom of movement.
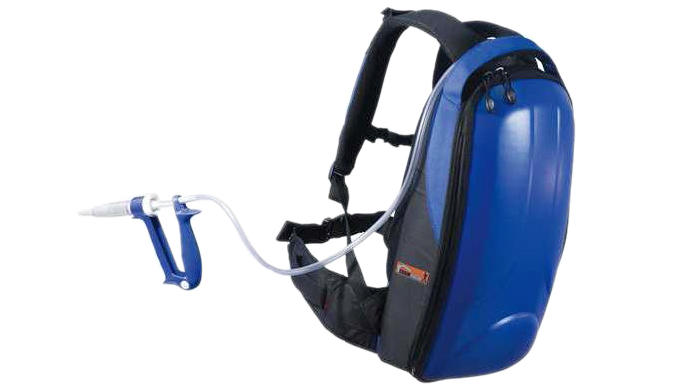

Production of a single-use needle guide
On behalf of a client specializing in computer-assisted urology and particularly in the diagnosis of prostate cancer, ARaymondlife accompanied the customer in the development of a single-use needle guide.
This class Is medical device is fixed to an endocavity 3D ultrasound probe allowing the biopsy needle to be guided.
Custom-made for the customer, the guide consists of 2 polycarbonate parts injected and assembled by ultrasonic welding.
The streamlined design has been optimized for maximum patient comfort.
This medical device complies with European Directive 93/42/EEC. ARaymondlife assisted its client in obtaining the CE marking and in the 510k procedure.
See our page about Certifications
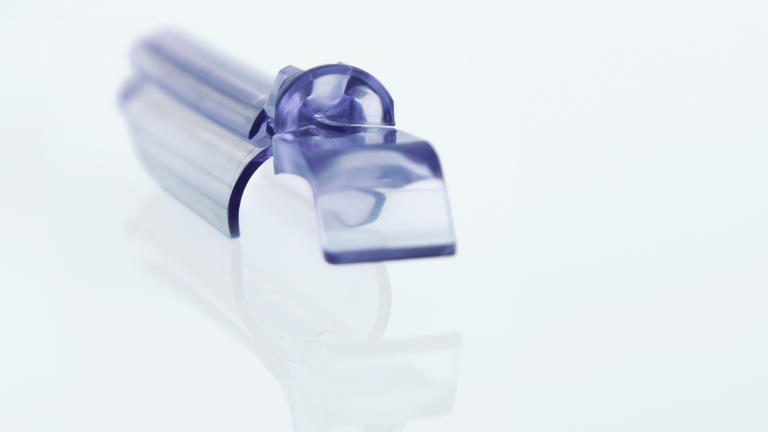
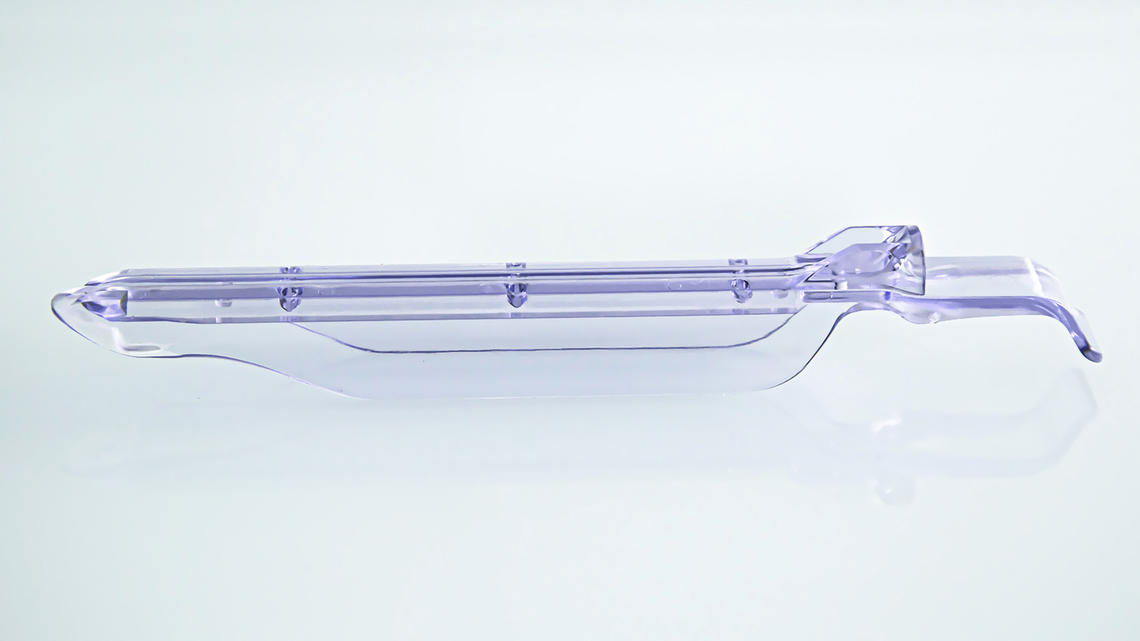
From machining to injection molding - PEEK
At a customer’s request ARaymondlife investigated the conversion of a part made by machining to injection molding.
The knowledge of the PEEK injection process along with ARaymondlife's mold-making expertise make this type of transfer possible.
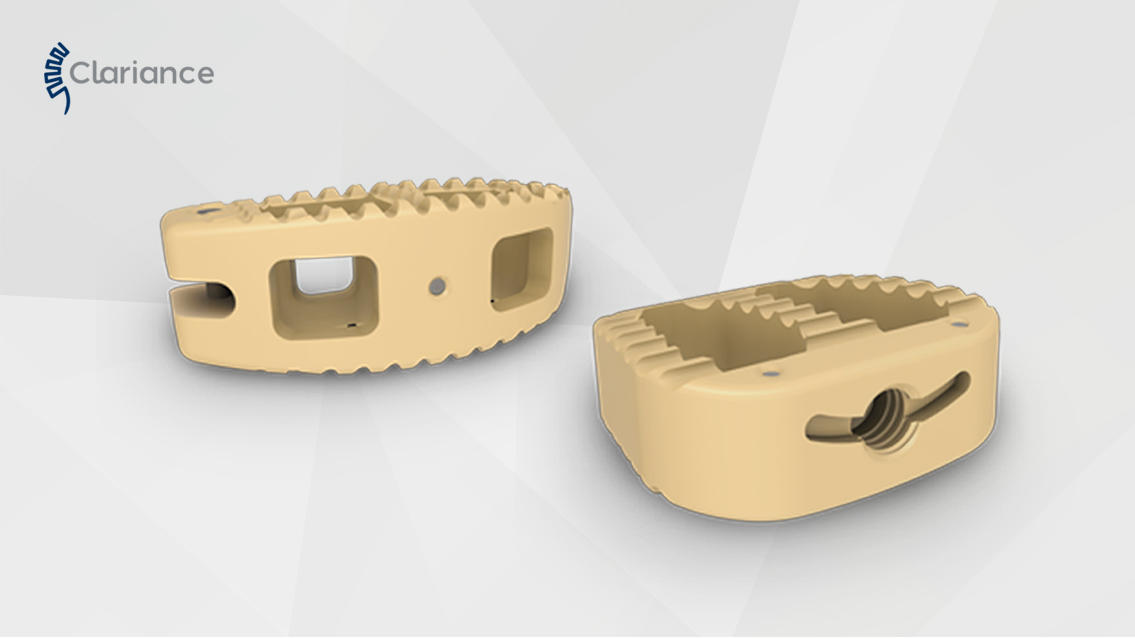